Case Study - Mobile Factory Tools & Multi Factory
Mobile Factory Tools & Multi Factory
Mobile Android App and Factory Separating ability
The challenge
Our client secured a major contract with a global tech firm to upgrade server hardware components for thousands of servers, located in high-availability centres around the world.
Due to the immediacy of the contract, however, our client’s operation simply wasn’t ready to deliver. The existing receiving, checking and processing systems were too slow, and the chances of backlogs and delays were high.
Our client’s customer also had highly challenging auditing and traceability requirements, adding to the complexity of the contract. Every component that passed through the factory’s manufacturing line had to be accompanied by a detailed audit history; this included the tasks performed on each component and by whom.
The sheer enormity of the data being generated by this contract was a real challenge. And if that wasn’t sufficiently daunting, the client had to add a range of new processes and operational enhancements without disrupting other factory operations.
To say the challenge and timescale were tight would be a huge understatement, but we approached the project with our usual zeal and determination.
Our solution
This was one of the most complex and challenging tasks we’ve ever undertaken. As a result, we thought it best to physically walk through every inch of the factory floor with our client.
What struck us was the need to reorganise the physical aspects of the factory in conjunction with managers and infrastructure installation specialists. If we were going to design a smooth and efficient flow without disrupting the client’s other operations, we needed to give everyone involved a say.
As we immersed ourselves more deeply into the existing operation, we also realised that a mobile, versatile approach was needed. Rather than tying operatives to their desks, we wanted to free them up — particularly at the check-in and packaging stages of the process.
After a painstaking assessment, and after taking copious notes and opinions, we created a solution that encompassed the following functions:
An efficient multi-factory set-up for multiple processes
We were able to devise a plan that split factories into separate entities. We took a logical approach to this process that allowed us to execute multiple processes simultaneously on a single site.
We knew that a significant workforce increase was inevitable, so we decided to split the factory into a series of sub-factories. As a result, managers were able to monitor their assigned sections without interfering with other processes taking place in the same facility.
An Android app
We used our findings to develop an Android app to manage the main system efficiently. We uploaded the app to handheld scanners, and they were used to perform a range of essential tasks.
- Component detection - We tracked and recorded the specific components entering the factory using manufacturer barcodes. Once the component was scanned, it was identified and assigned to a specific manufacturing journey. In addition, a set of rules was attached to the component — accompanying it around the factory.
The system we designed, created and executed allowed factory managers to design complex, customised task routes in conjunction with the end client. - Real-time feedback and auditing - Factory operatives could now scan components in and out of specific tasks as they made their way through the factory. Every task, process and movement was tracked and logged. And issues were immediately raised with the appropriate supervisor.
- Packaging and dispatch - Once the component was complete, an operative could perform a final scan to generate the correct dispatch and packaging information. This was a crucial part of the entire process, as every component had to be sent to a specific data centre — and there were several of them around the world.
Once the packaging was generated for a component, a digital audit report was automatically sent to the client. This saved both our client and their customer a significant amount of time and money.
Enhanced performance and reporting
Our client had to cope with a huge and sudden increase in data when they took on this huge contract. This meant we had to devise a system that would make data management and reporting efficient.
We helped managers analyse the performance of operatives and processes by giving them quick and unhindered access to the relevant reports. This approach made identifying issues and improving efficiencies significantly easier.
Finally, we created a system that integrated all of the process and performance reports to ensure our client could analyse the data on a per-factory basis or for the operation in its entirety.
The results
We always get a great deal of satisfaction when we’re able to dramatically increase the efficiency of a manufacturing operation. But this particular project will always be one of our greatest achievements. Once we were able to assess the efficacy of our system, it emerged that factory throughput was up by 300%.
We removed bottlenecks and inefficiencies throughout the manufacturing process with the use of mobile apps. And the versatility we built into the apps makes the addition of new functionality in the future a relatively quick and simple task.
We took one factory and split it into a series of sub-factories — each with its own processes and responsibilities. The great news is that we can adapt this approach to other operations, giving us the ability to manage multiple factories without the need to create new systems. Not only does this reduce overall maintenance, but it also allows managers to access real-time data from a single task or for an entire operation.
Our client can now create a new sub-factory with a click of a button. And the inherent adaptability that’s built into our solution can be used for prototypes and training.

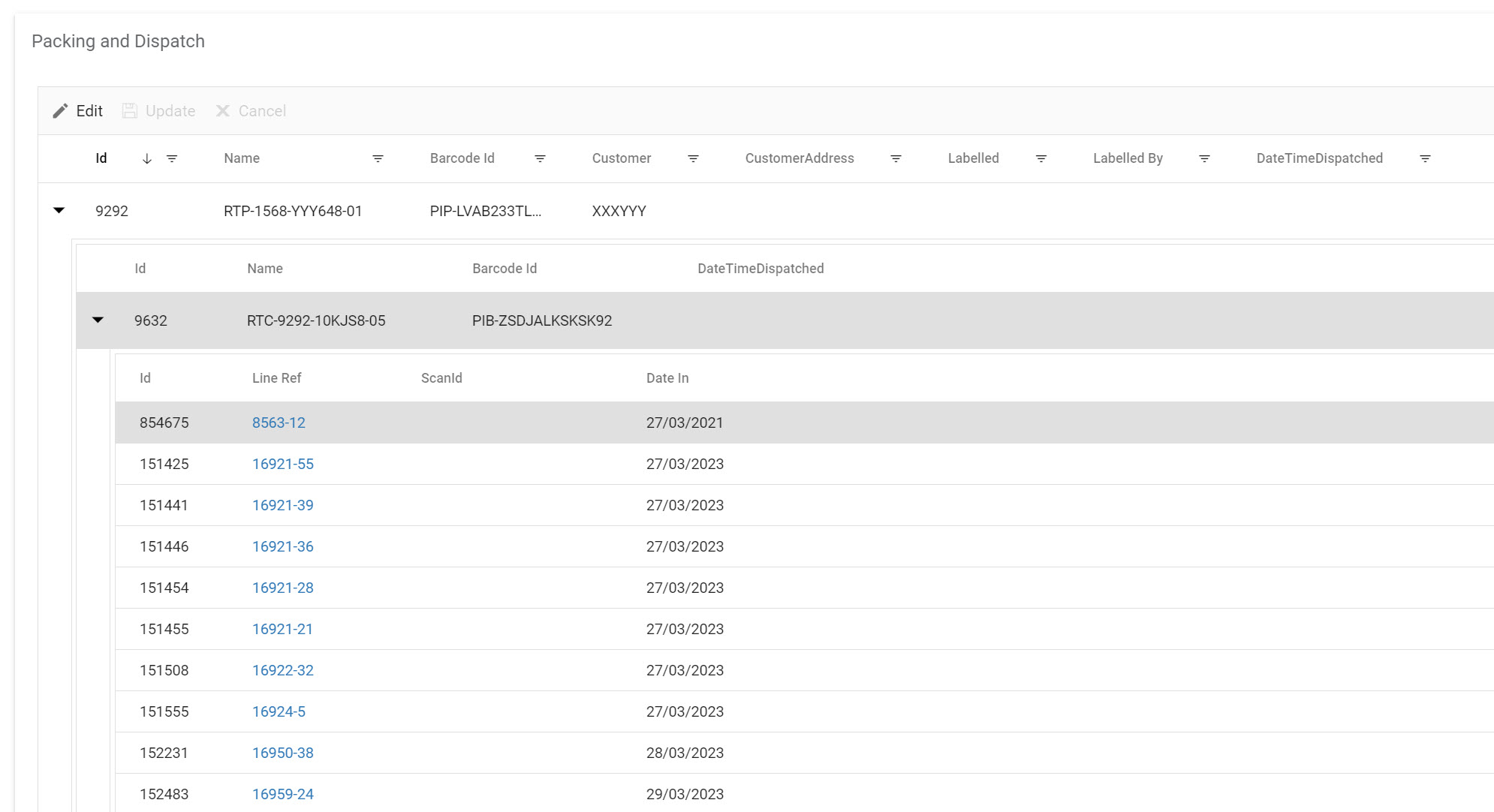
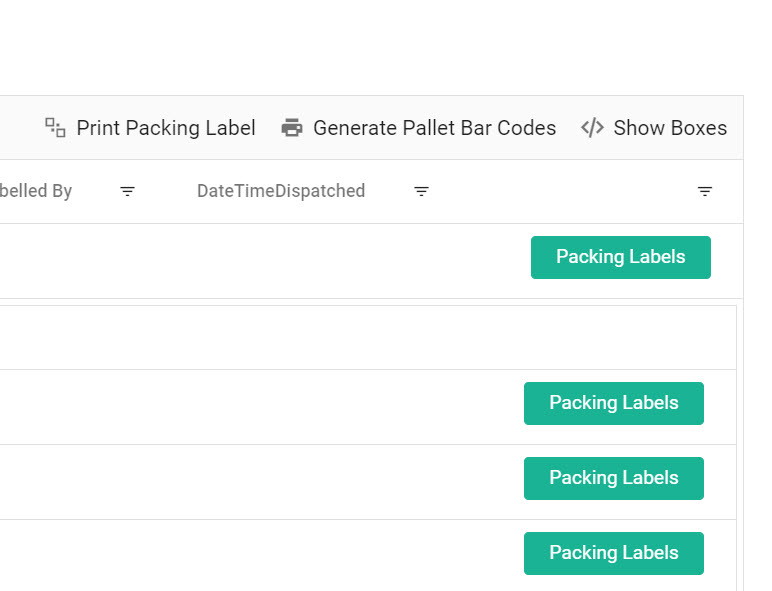