Case Study - End to End Traceability & Auditability
Factory End to End Traceability
Tracking the entire journey of electronic components — from arrival to shipping
The challenge
We were approached by a client to create a more transparent and auditable component journey through their factory operation. The client was an electronic manufacturing business that provides a range of highly reliable services for the defence, military, aerospace and fossil fuel industries.
This is an area that requires complete traceability throughout the manufacturing process. From the moment a component arrives at the factory to the moment it’s shipped to the client, its path must be tracked and recorded. This process must be verified by a series of rolling on-site audits to satisfy the customers’ highly complex specifications.
Our client needed our help because they had a contractual obligation to carry out the manufacturing process in strict compliance with the agreed production standards. Every aspect of the process had to be recorded and backed up by detailed records of each task.
At the time of starting this challenging project, the client was using an inefficient system that involved linking a ‘traveller’ set of paper documents with all the components as they moved through the production line. This method of providing traceability and transparency was causing our client several problems.
- A paperwork overload - The most complex tasks within the operation involved hundreds of documents accompanying components as they made their way through the production process. As well as the physical challenge of managing this mountain of paperwork, the client also had the problem of storing and archiving documentation for future audits.
- Missing paperwork - It’s not surprising that, given the enormous amount of paperwork involved, some essential documents would go missing from time to time. As the processes became more complex, the missing paperwork became more of an issue for audits and transparency. Our client was concerned that this might affect customer trust levels.
- Human error - It would take just one factory worker to forget or mislay an important document for the entire operation to be disrupted. As there was no system in place to pick up these errors in real-time, additional workers would need to check documents at various stages throughout the process. This was cumbersome, inefficient and very costly.
- Complex documentation recalls - Whenever the client or someone in the manufacturing team raised a query, a time-consuming and costly process to locate and check the relevant documents would be performed manually. Put simply, this was directly affecting the client’s profitability and customer relationships.
Our solution
The only way we were ever going to deliver a bespoke solution to such a complex problem was to get onto the factory floor with our client and their team. We had to go back to the drawing board and dismantle the process before building it again from scratch. As a result, however, we were able to create customised web and mobile applications that delivered the following functions:
- Workflow designer - We worked side-by-side with our client and their team to assess the challenges and create a workflow designer that would manage factory processes and satisfy auditing requirements. The system we created was able to manage a range of tasks, including the processing of inspection reports, consumables checks and X-ray images. This was backed up by a rules-based process that ensured documentation was completed correctly — with full accountability.
- Exception handling - Our new system flagged operative errors to management in real time. Supervisors were now informed of the ‘expected behaviour’ — along with what happened. This intuitive approach to error management nipped problems in the bud and allowed for quick and decisive remedial action.
- Paperless processing - One of our top priorities was to remove the paper mountain from the client’s manufacturing processes. Our system digitised all the relevant documentation and permanently linked them to specific tasks. This essential data — which included X-ray images, photos, inspection data and other vital information — was then recorded and stored in a secure location for future audits.
- Instant recall - The system we designed was able to recall specific documents in a matter of seconds. All the user needs to do now is identify the relevant task. This is saving our client a huge amount of time and resources.
- Documentation bundles - We were able to deliver a much greater level of transparency and traceability for our client. In turn, they were able to provide every customer with a full documentation bundle for every product that passed through the manufacturing process. There’s now a complete record that includes every step and procedure involved in the manufacturing process — delivered to customers with their purchases.
- Full traceability and accountability - Every stage of the manufacturing process is now fully traceable in seconds. This has delivered an unprecedented level of accountability within the operation, which gives us all an enormous sense of satisfaction.
The results
End-to-end traceability was the ultimate objective of this project. Our web-based system delivered an adaptable solution that was able to manage all of our client’s factory processes. We were particularly proud of this achievement, as the bespoke solution we delivered empowered thorough auditing procedures while allowing the client to move to a much more efficient paperless system.
We were also delighted to deliver a system that made recalling specific documents a quick and simple process. As a result of our work, the client is now able to manage and rectify errors swiftly and decisively — and that has made their entire operation much more efficient.
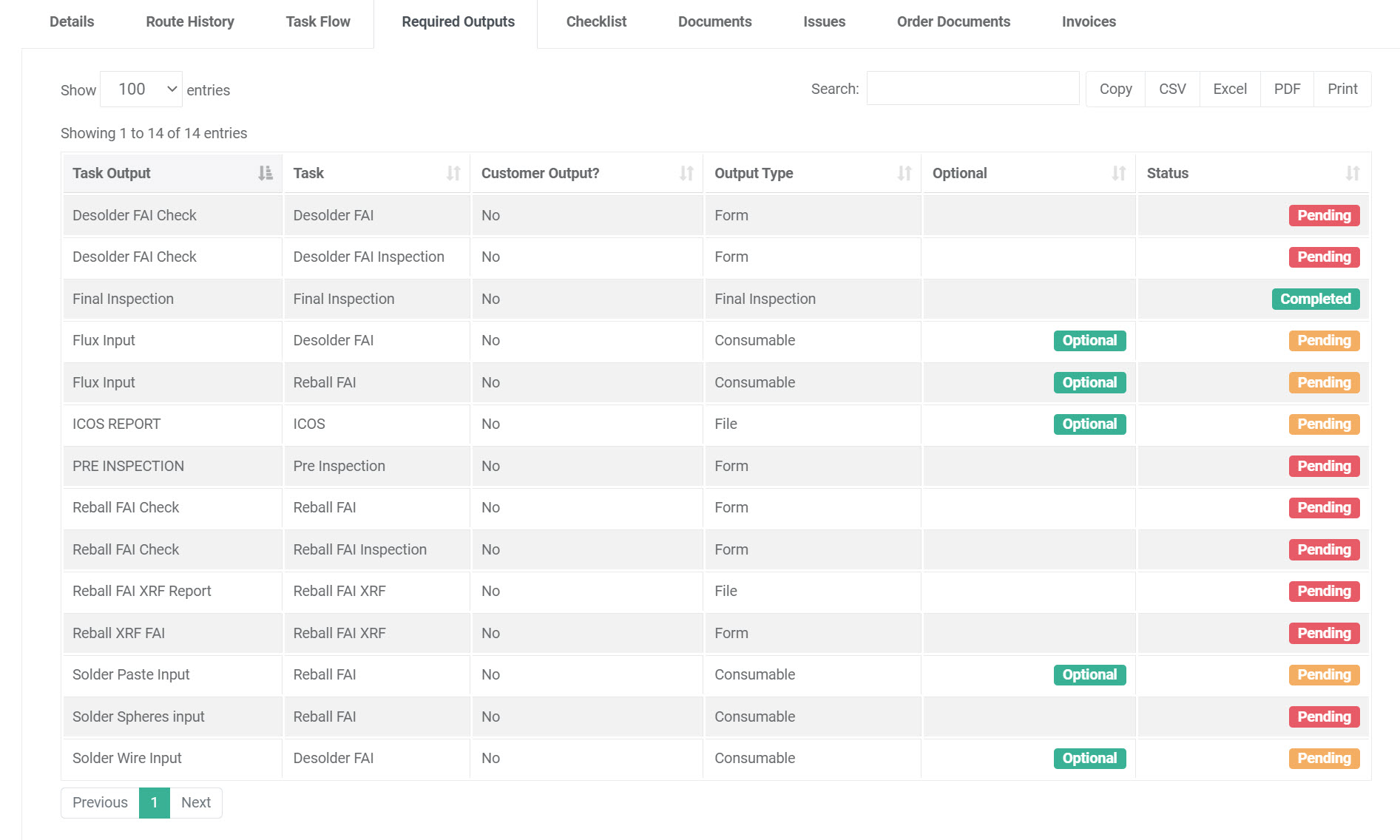